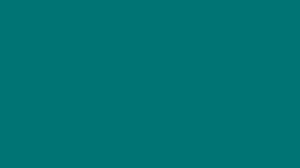
What is Machine Tending?
When you think of the manufacturing industry, your mind likely fills with images of conveyor belts, robotic arms, or even the sounds of tools and parts as machines craft products. In part, those images may be accurate, but where are the people? If the image in your mind doesn’t include people loading the machines, then you’re missing an essential element of the process– machine tending.
More recently, advanced robotics has revolutionized machine tending, offering manufacturers improved efficiency, precision, and safety. Understanding the intricacies of machine tending can help manufacturers make informed decisions about integrating automation into their operations, ultimately driving productivity and competitiveness. Of course, people are critical throughout the entire process.
Understanding Machine Tending
Machine tending is a vital part of any manufacturing business, but that doesn’t mean it’s a simple task. Machine tending is the process of loading raw material into a CNC (Computer Numerical Control) machine and unloading the finished part. This process is essential for the continuous and efficient operation of various types of industrial machinery, including CNC machines, injection molding machines, and assembly lines to name a few.
The role of a machine tender includes not only the physical handling of materials but also monitoring the machine's performance, conducting quality checks, and ensuring that the production process runs smoothly. During this process, the mechanic tends the machine in order to limit downtime and keep production moving.
Machine tending relies on operators and tenders to monitor the machinery during operation. After a setter prepares a machine for production, an operator observes the machines and the products it creates. Throughout this, operators may need to load the machine with materials for production or adjust the machine’s speeds during production in order to maintain the quality of the finished product.
Machine Tending Challenges
As you can imagine, the traditional machine tending process is long and tedious. It also presents several challenges despite this being a crucial part of standard manufacturing processes.
As manufacturing technology advances, machines become more sophisticated and require precise handling and monitoring. This then requires a high level of expertise from operators, which can be hard to find in an already shrinking labor pool. Plus, any downtime caused by errors or maintenance issues can lead to significant production delays and increased costs. Ensuring that machines are consistently tended to and maintained is crucial for avoiding these disruptions and ensuring a smooth production flow.
Additionally, effective machine tending is essential for maintaining operational efficiency and product quality. Inadequate tending can result in machine malfunctions, production halts, and higher rates of defective products. These issues not only increase operational costs but also affect a company’s reputation and competitiveness in the market. Consequently, manufacturers must prioritize finding solutions to these challenges to sustain productivity and maintain high standards of quality.
One solution to these challenges is the adoption of automated machine tending systems. Automation can alleviate the burden on human workers by handling repetitive tasks with greater accuracy and consistency. This not only reduces the risk of human error but also allows for continuous, round-the-clock operation, thereby maximizing productivity.
The Roll of Robots in Machine Tending
Like other industries, a major goal in the manufacturing world is to boost efficiency while maintaining or improving outcomes. And to do so, robots and automation technology are stepping in. The primary role of robots for machine tending specifically is to enhance efficiency, consistency, and safety, addressing several challenges inherent to human-operated machine tending.
To boost efficiency, these machine tending robots increase CNC machine uptime and utilization, which also limits the possibility for human error. By eliminating loading and unloading machines from the responsibility of mechanics, manufacturing businesses can rest easy knowing the parts are all collected safely and employees can focus on tasks that demand careful attention.
Speaking of employees, finding skilled CNC mechanics has become increasingly challenging. As more businesses compete for a limited pool of qualified candidates, the likelihood of quickly filling an open position is minimal. Fortunately, a reliable machine tending system can effectively bridge this gap, allowing overburdened mechanics to address other tasks at hand with a clear mind.
Benefits of Robotic Machine Tending
The shift from manual to robotic machine tending brings numerous benefits, such as increased operational efficiency, consistent product quality, and enhanced workplace safety. As the manufacturing industry continues to evolve, the integration of robotic machine tending systems is becoming a vital component for companies aiming to maintain a competitive edge.
Continuous Operation
One of the significant advantages of using robots for machine tending is their ability to operate continuously without fatigue. Robots can perform repetitive tasks with high precision and consistency, reducing the likelihood of errors that can occur due to human factors such as tiredness or distraction.
This continuous operation not only increases the throughput but also ensures the quality of the manufactured parts remains consistently high. In industries where precision is crucial, such as aerospace or medical device manufacturing, this consistency is particularly valuable.
Enhanced Precision
Robots are capable of performing tasks with a high degree of accuracy, ensuring that each part is handled in exactly the same way every time. This level of consistency is difficult to achieve with manual labor, where human error can lead to variations in product quality. Thanks to preprogrammed inputs, robotic machine tending helps manufacturers meet stringent quality standards and reduce the rate of defective products.
Improved Safety
Machine tending often involves exposure to hazardous conditions, including high temperatures, heavy machinery, and repetitive movements that can lead to musculoskeletal injuries. In fact, repetitive stress injuries are among the most common types of injuries experienced by factory workers. So, by delegating these tasks to robots, manufacturers can protect their workforce from potential injuries and associated downtime, leading to a safer and more productive workplace.
Increased Profitability
Minimizing accidents and maximizing throughput contributes to increased profit margin per part, allowing manufacturing businesses to continually expand and grow. By leveraging machine tending robots and programming them to work beyond the standard 8 hour shift, automation offers an excellent opportunity to produce more parts at a lower cost per part. As a result, there will be less burdensome work placed on mechanics and increases in productivity and profits.
Flexibility and Adaptability
Modern robots are equipped with advanced sensors and machine learning algorithms that allow them to adapt to different tasks and handle a variety of materials and parts. This adaptability makes it easier for manufacturers to switch between different production lines and customize their processes to meet changing market demands. In other words, the integration of robots in machine tending can lead to more agile and responsive manufacturing operations.
6 Applications of Automated Machine Tending
Machine tending processes are utilized across all kinds of industries. And where there’s machine tending, there’s also an opportunity for robotic automation. Businesses who aren’t yet incorporating automated machine tending technologies into their standard operations are likely missing out on the efficiencies that come with these advancements.
Automotive Manufacturing
In the automotive industry, automated machine tending plays a pivotal role in streamlining production processes and ensuring high-quality output. Robotic systems are used extensively for tending CNC machines that produce engine components, transmission parts, and other critical automotive elements. By automating the loading and unloading of these machines, manufacturers can achieve a higher level of precision and consistency, essential for maintaining the stringent quality standards of automotive parts.
Additionally, robotic machine tending reduces cycle times, allowing manufacturers to increase their throughput and meet the high demand for automotive components. This automation also enhances workplace safety by minimizing human interaction with heavy machinery and hazardous materials.
Metalworking and Machining
Metalworking and machining industries benefit significantly from automated machine tending, particularly in operations involving CNC milling, turning, and grinding. Robots can handle raw metal stock and finished parts with a high degree of accuracy, reducing the risk of defects and rework.
Beyond this, robotic machine tending can be easily integrated with other automated processes, such as quality inspection and part cleaning, to create a seamless and efficient production line. This integration helps metalworking shops to optimize their workflows, reduce labor costs, and improve overall operational efficiency.
Plastics and Injection Molding
When it comes to plastics and injection molding, machine tending is best utilized when handling the repetitive and labor-intensive task of managing molds and finished plastic parts. For this application, robots are used to load raw plastic pellets into injection molding machines and to remove completed parts once they have cooled and solidified. This automation not only speeds up the production process but also ensures that parts are handled carefully, minimizing damage and defects.
Electronics Manufacturing
In the electronics manufacturing sector, precision and cleanliness are paramount. So, automated machine tending systems are equipped to handle delicate electronic components during the assembly process, such as placing circuit boards into manufacturing equipment and removing them after soldering or testing.
When developing products for the electronics industry, it’s important that components are products under optimal conditions. Fortunately, robots can operate in cleanroom environments, reducing the risk of contamination or defects. Moreover, robots can be equipped with vision systems to perform intricate tasks with high precision, making them ideal for handling small, delicate parts that are common in electronic devices.
Food and Beverage Industry
In the food and beverage industry, automated machine tending is leveraged to manage vital tasks such as loading ingredients into processing machines, packaging finished products, and performing quality checks. Robots can handle these tasks with speed and consistency, reducing the risk of contamination and ensuring that products meet safety and quality standards.
And, in this industry in particular, hygiene is critical in order to protect the health and safety of consumers. To address this, machine tending robots can be designed to operate in sanitary conditions and be easily cleaned.
Additionally, the use of robotics in machine tending also allows food and beverage manufacturers to respond quickly to changes in demand, as automated systems can be reprogrammed and reconfigured to handle different products and packaging formats. This flexibility, combined with the efficiency of robotic automation, helps manufacturers to maintain high levels of productivity and adaptability in a competitive market.
Aerospace Manufacturing
Aerospace manufacturing demands the utmost precision and reliability, given the critical nature of aerospace components. Automated machine tending is integral to producing parts such as turbine blades, structural components, and precision fittings. Robots handle the loading and unloading of machining centers, ensuring that parts are processed without human error.
Additionally, automated machine tending systems can operate around the clock, significantly increasing production rates and enabling aerospace manufacturers to meet tight deadlines. The consistent quality provided by robotic systems also helps in reducing the need for rework and ensuring compliance with stringent regulatory requirements.
Getting Started with Automated Machine Tending
If it's not clear to you yet, know that automated machine tending is the solution to enhanced workplace safety, efficiency, and productivity. So much so that automation gives any job shop or factory a leg up in the competitive world of manufacturing. By incorporating these processes and technologies, you minimize human error, maximize CNC efficiency, and increase throughput.
To get started, be sure to check out AWR’s range of robotic automation products, including:
- DC Series: Increase CNC machine utilization with a lathe tending machine that can hold up to 180 parts with its smallest optional template.
- RC Series: Holding up to 166 small-diameter parts, the RC Series accommodates parts up to 11 inches in length and can fill an extra shift in your shop.
- VBX Series: Increase CNC production with the VBX series, capable of automating multiple different OP10/OP20 parts with no need for human interference.
Essentially, automated machine tending is the right step for increasing CNC productivity and improving machine shop processes. If you’re interested to see if one of our machine tending solutions can benefit you, contact the AWR team for a free demo with your part.