If you use a smartphone, you have the ability to control your music, set automatic reminders, share information across devices, and in some cases, even turn on and preheat your oven. For all of those functions, you’re communicating with apps in order to accomplish goals in various aspects of your life. The Internet of Things (IoT) aims to do something similar.
When IoT is applied to manufacturing settings, AKA smart manufacturing, businesses unlock a world of possibilities when it comes to the way equipment communicates with one another and how data can be used to streamline operations.
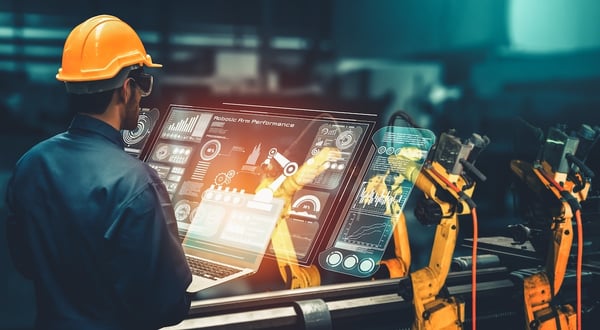
Quick Links
- What is IoT?
- Understanding IoT in Smart Manufacturing
- Key Benefits of IoT-Integrated CNC Automation
- Challenges and Considerations for IoT Adoption in CNC Automation
- Achieve Smart Manufacturing Goals with CNC Automation
What is IoT?
The Internet of Things is transforming industries by connecting machines, devices, and systems to gather and share data in real time. At its core, IoT involves embedding sensors and connectivity into physical equipment, allowing them to communicate with each other and with centralized systems. This constant flow of data enables businesses to monitor performance, detect inefficiencies, and make informed decisions faster than ever before.
Think of IoT as a network of smart devices that collect and exchange data without requiring human intervention. These devices can range from everyday consumer gadgets, like smart thermostats that adjust temperature based on usage patterns, to complex industrial machinery that self-diagnoses issues before they become critical failures. The power of IoT lies in its ability to turn raw data into actionable insights, automating decision-making and optimizing operations across various industries.
In industrial settings, IoT enhances visibility and control over production processes by enabling real-time monitoring and remote management. Over time, the continuous feedback loop generated by IoT devices enables companies to optimize their processes, reduce waste, and boost overall efficiency.
Understanding IoT in Smart Manufacturing
In manufacturing, IoT takes this concept a step further by creating “smart factories” where machines, sensors, and software work together to optimize production. This industrial application of IoT, known as the Industrial Internet of Things (IIoT), enhances visibility, efficiency, and automation across manufacturing operations. IIoT relies on several key components to function effectively:
- Sensors and Edge Devices: These are embedded into CNC machines to monitor critical parameters such as spindle speed, tool wear, temperature, vibration, and power consumption. They provide real-time data on machine performance and operating conditions.
- Connectivity: Sensors and devices communicate through industrial networking systems like Wi-Fi or 5G, ensuring seamless data transfer between machines, cloud platforms, and enterprise systems.
- Cloud Computing: Data collected from CNC machines and robotic systems is sent to cloud-based platforms where it’s then stored, processed, and analyzed. Cloud infrastructure allows manufacturers to access data from anywhere, allowing for remote monitoring and control.
- Data Analytics and AI: Advanced analytics tools process vast amounts of machine data to identify patterns, detect inefficiencies, and predict maintenance needs. These AI-driven insights help manufacturers optimize production and reduce downtime.
The combination of IIoT with automated robotic machine tending solutions takes manufacturing to the next level. Robots can operate with minimal human intervention while continuously adjusting processes based on IoT-driven insights. For example, if a CNC machine’s temperature exceeds safe limits, an automated system can slow down operations or trigger a maintenance alert before any damage occurs.
By embracing IIoT and CNC automation, job shops and factories can move toward fully connected, data-driven manufacturing. The result? Increased uptime, reduced scrap, lower operational costs, and a more agile production environment that can quickly adapt to changing demands.
Key Benefits of IoT-Integrated CNC Automation
The integration of IoT with CNC automation isn’t just about making machines smarter–it’s about unlocking new levels of efficiency, precision, and reliability in manufacturing. By leveraging real-time data, predictive insights, and remote accessibility, manufacturers can significantly improve their operations. Here’s a closer look at some of the most impactful benefits:
Real-Time Machine Monitoring & Predictive Maintenance
One of the biggest advantages of IoT in CNC automation is the ability to track machine performance. IoT sensors embedded in CNC machines monitor critical factors like spindle speed, vibration levels, temperature, and tool wear. If any anomalies arise, such as excessive heat or irregular tool wear, the system sends instant alerts, allowing operators to take proactive action before issues escalate.
Predictive maintenance takes this a step further by using AI-powered analytics to forecast potential failures. Instead of waiting for a breakdown, manufacturers can schedule maintenance precisely when it’s needed, reducing unplanned downtime and extending equipment lifespan. This means fewer disruptions, lower repair costs, and a more efficient production schedule.
Improved Operational Efficiency
Data is a powerful tool in manufacturing, and IoT turns raw machine data into actionable insights. By analyzing real-time performance metrics, manufacturers can optimize machine cycles, reduce idle time, and improve overall equipment effectiveness (OEE).
Additionally, adaptive automation powered by IoT allows CNC machines and robotic tending systems to adjust dynamically based on job schedules, material availability, and demand fluctuations. This results in better workflow coordination, increased throughput, and more responsive production planning.
Enhanced Quality Control
Precision is everything in CNC machining, and IoT plays a crucial role in ensuring consistent, high-quality output. By continuously monitoring cutting parameters, tool conditions, and environmental factors, IoT-enabled systems can make real-time adjustments to maintain accuracy.
Plus, these tools can detect any defects, such as surface imperfections, further enhancing quality control. This reduces scrap rates, minimizes rework, and ensures that every finished product meets exact specifications.
Remote Management
With cloud-based CNC monitoring, manufacturers are no longer tied to the factory floor and can instead focus on lights-out factory goals. IoT allows for remote access to machine data, enabling offsite management through mobile apps and web-based dashboards. Operators can check machine status, review performance reports, and even make process adjustments from anywhere.
Challenges and Considerations for IoT Adoption in CNC Automation
While the benefits of IoT-integrated CNC automation are substantial, adopting this technology comes with its own set of challenges. Manufacturers must consider factors such as security, system integration, and investment costs when implementing IoT solutions.
Security Concerns and Data Protection
With IoT connecting CNC machines to cloud networks and remote systems, cybersecurity becomes a top priority. Data breaches or cyberattacks could compromise sensitive production data, disrupt operations, or even lead to intellectual property theft.
To mitigate these risks, manufacturers should implement strong encryption protocols, multi-layer authentication, and network segmentation to protect IoT-enabled CNC systems. Additionally, regular software updates and cybersecurity training for employees can help safeguard against potential threats.
Integration Challenges with Legacy CNC Machines
Many factories still rely on older CNC machines that weren’t designed for IoT connectivity. Retrofitting legacy equipment with modern sensors and network interfaces can be complex, requiring custom solutions or middleware to bridge the gap between old and new systems.
To ensure a smooth transition, manufacturers should assess their existing infrastructure and partner with a solution provider that’s experienced in IoT devices for manufacturing, which ultimately helps streamline the adoption process.
Initial Investment vs. Long-Term ROI
Adopting IoT technology requires upfront investment in hardware, software, and infrastructure upgrades. While the cost may seem high initially, the long-term benefits–such as reduced downtime, higher productivity, and lower maintenance expenses–often outweigh the investment.
A well-planned IoT adoption strategy focuses on scalable implementation, starting with high-impact areas like predictive maintenance and real-time monitoring before expanding to more advanced automation features. By taking a phased approach, manufacturers can gradually integrate IoT without disrupting operations or straining budgets.
Achieve Smart Manufacturing Goals with CNC Automation
While implementing IoT in CNC automation requires careful planning, the rewards make it a worthwhile investment. As factories continue to embrace digital transformation, IoT will play a key role in shaping the future of smart manufacturing, enabling job shops and large-scale production facilities alike to stay competitive in an increasingly data-driven industry.
Among larger smart manufacturing goals, CNC automation is essential for streamlining efficiency and accuracy in part production. With Automation Within Reach, job shops and manufacturing businesses can enhance their CNC machining capabilities with robotic machine tending solutions. So, if you’re looking to enhance operations through continuous machine tending, you’re in the right place.
Reach out to an automation expert today to learn more about CNC automation for smart manufacturing goals!